EXTRUSIONs
The Extrusion Division of Pipeline Equipment, Inc. is one of only a few companies in the U.S. with the capacity and experience to produce single and multiple outlet headers utilizing the closed-die forming process. The company was founded in 1997 and has more than 50 years of managerial experience in extruded headers.
Extrusions can be manufactured in a wide variety of carbon, stainless, nickel, chrome-nickel alloys and many other ferrous and non-ferrous materials. Extrusions provide butt-weld joints that are easily radiographed and save fit-up and welding time.
PROCESS
The external die restrains the header pipe and controls the outside diameter of the outlet, while the precise inside diameter and wall thickness are determined by the punch. The punch extrudes or pulls the base metal through the die by means of a proprietary hydraulic process. Depending upon the header material, the outlets may be cold or hot-formed. The closed die manufacturing process is applicable to a broad range of materials, outlet sizes and wall thickness and provides flexibility in outlet applications.
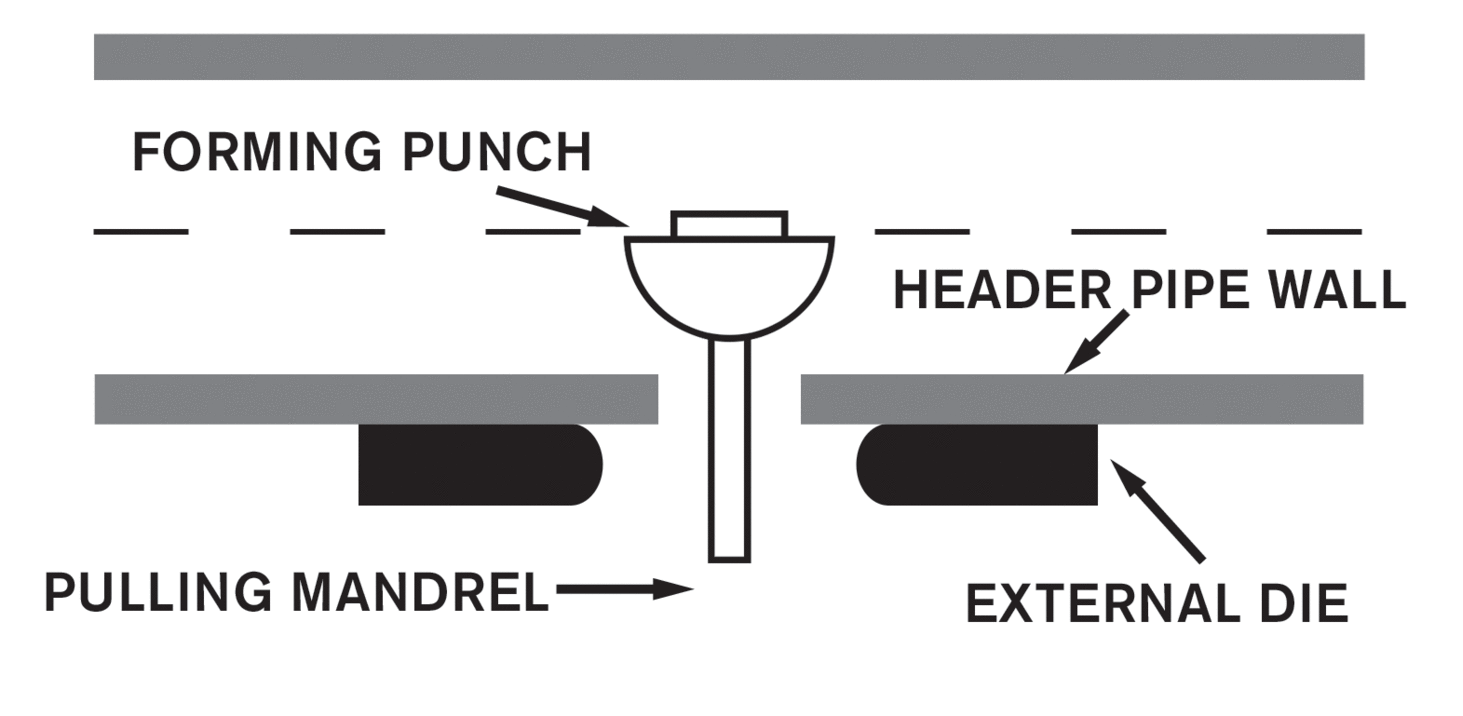
BENEFITS
Flexibility
Outlet configuration and location, material selection, and varied industrial applications are all a part of the flexibility provided by extrusions. Utilizing extrusions in the design process reduces erosion, pressure drops and stress concentration. Extrusions can be produced to meet the code requirements of pipeline and gas transmission, chemical manufacturing and power generation applications.
Reduced Cost
Extruded outlets save fabrication costs by reducing fit-up, welding and inspection time and are more durable than stub-in branch construction.
Reliability
Outlet tolerances can be closely produced and maintained. Extrusions eliminate the need for reinforcement pads, provide butt-welded joints and allow complete radiographic inspection.
Longevity
Extruded headers have a longer lifespan due to less erosion wear and a lower repair cost than conventionally constructed headers. Additionally, extrusions reduce maintenance costs due to their durability and corresponding reduction in lost production time.
Take the Next Step With PEI
Call Us
Call PEI's main office and we will connect you with the right person to answer your questions.
Find Your Rep
Find your PEI representative on our Rep Finder page to speak with the PEI rep closest to your location.
Request a Quote
Watch your profits and efficiency soar. You’ll expand faster than you ever thought possible.